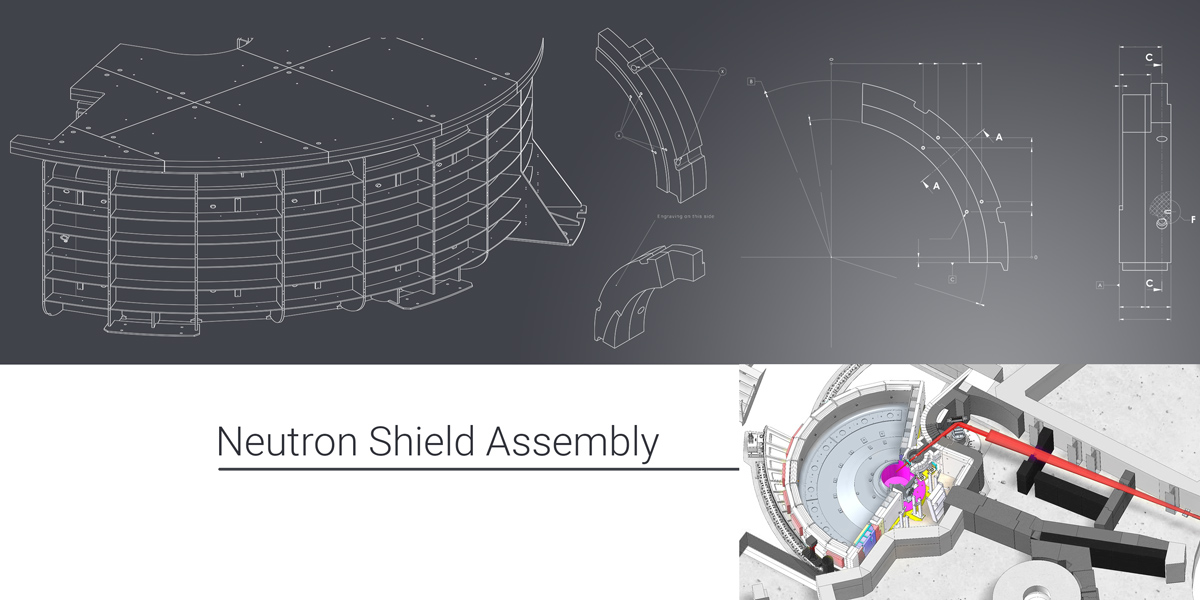
Neutron Shield Assembly
The decisions while designing a neutron shield can be down to the smallest details: JCS Nuclear was approached to design a large bespoke neutron shield which would fit together to complete the complex shielding array that surrounds the ILL Panther Beam Dump.
The Challenge
In 2017 – JCS Nuclear was approached by the Panther Shielding team at ILL (Institut Laue Langevin) to explore how JCS might supply a large volume of bespoke finished parts of JCPE5 (Boron loaded polyethylene neutron shield material) which would fit together to complete the complex shielding array that surrounds the ILL Panther Beam Dump.
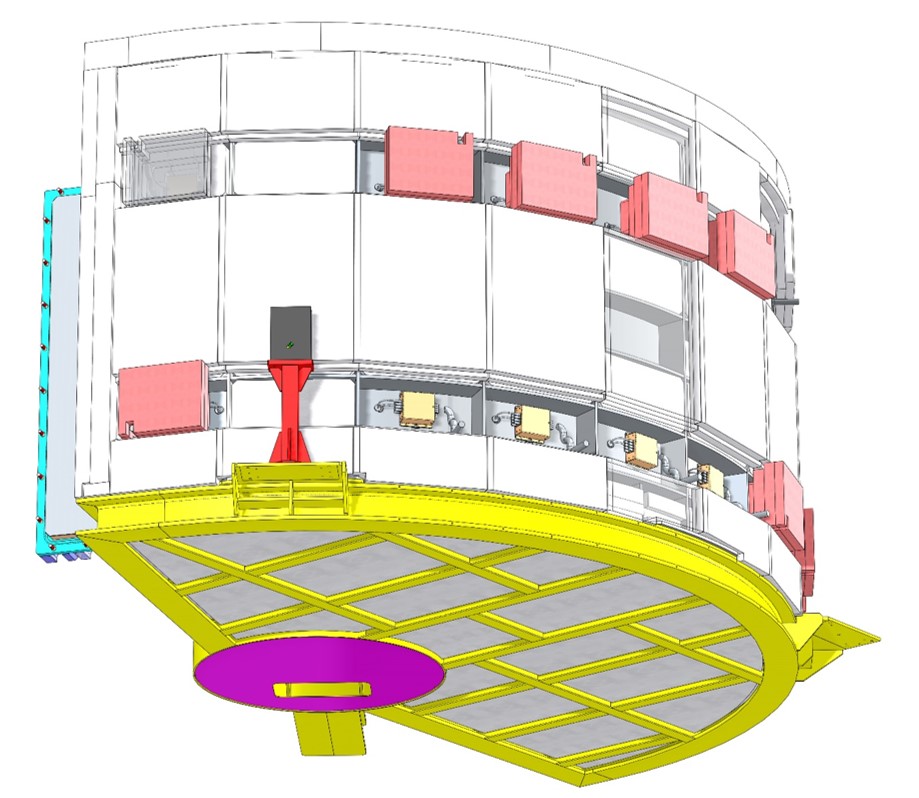
After several technical conference calls, the ILL team came to visit JCS in the UK. Here, they could tour the factory, learn about previous projects delivered by JCS and discuss, in detail, the challenges of the ILL shielding project.
JCS was able to demonstrate, by examples, our capabilities to handle large volume shielding projects, retain a high level of QA and ultimately provide considerable value to the customer.
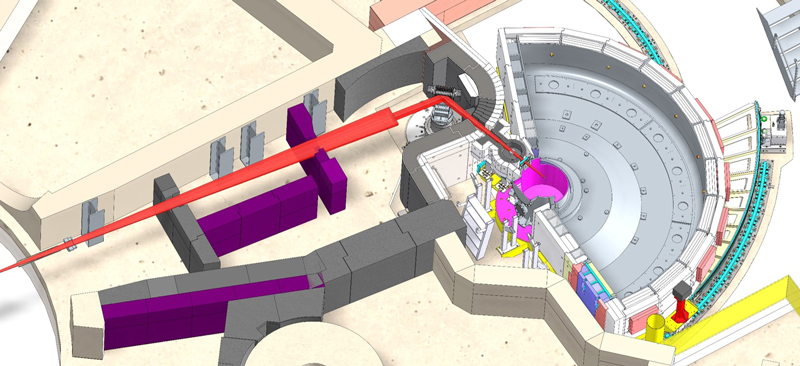
Traceability
Traceability of all materials (from resins to boron additives) is fundamental for QA records, as was the required inspection of each item part. vast records were kept and issued to the customer. All pre-delivery inspections were carried-out (both in-person and by video conference), before releasing the total consignment to ILL.
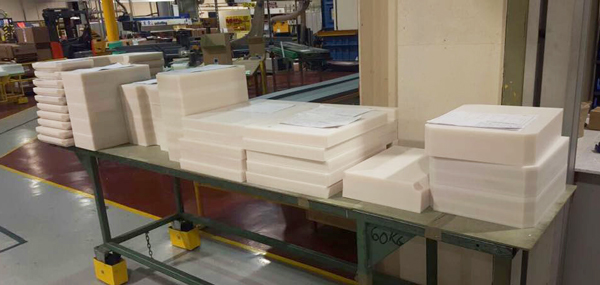
The Details
The decisions while designing a neutron shield can be down to the smallest details, for instance, how to secure the shielding to any structure and the machined blocks to their counterparts while eliminating shine-paths and any unplanned interactions.
Depending on the size of the part, we can peg with “dowels” made from the same material or as in this picture, they can be held together with a stainless threaded bar. It all depends on the application and what materials are welcome into the area.
We frequently machine a male/female step or join in between layers to enhance shielding properties of the parts before pegging together.
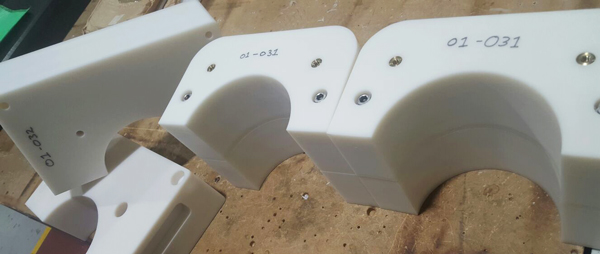
Delivery
To simplify assembly planning, ILL inspection and part number ID for goods inwards, each part was individually labelled and packed per lot number.
Each section of the shield was shipped to the customer in the agreed build order to aid the construction and ease storage capacity.
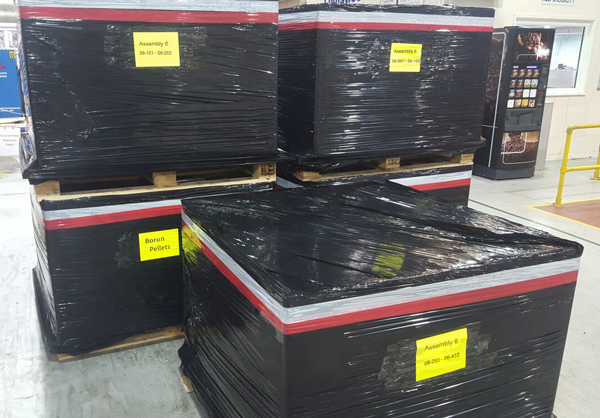
Partnership
The project was a resounding success and very much treated as a collaboration project between ILL and JCS – drawing packs for each lot were issued by ILL, from which JCS provided a per-item price list (many thousands of parts). Production drawings were issued, JCS would then schedule the delivery plan per lot.
Since delivering the panther beam dump assembly, JCS has been nominated as the preferred supplier for 5% Boron Polyethylene and has now delivered on many significant projects.
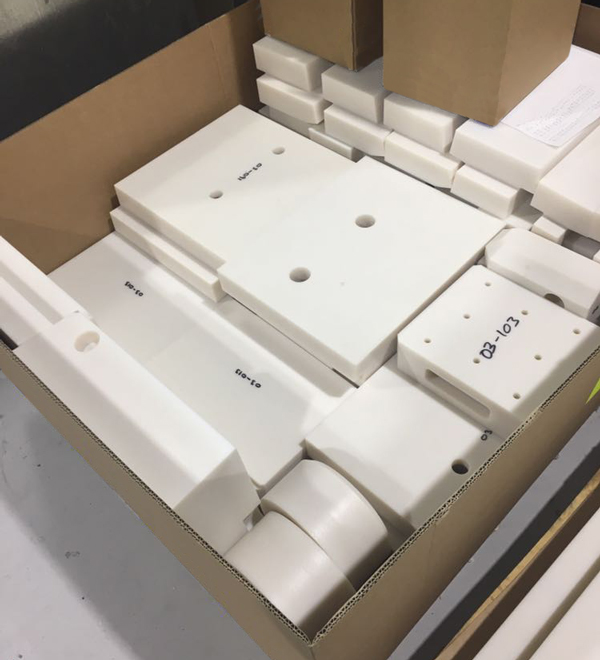
Machined Blocks Awaiting QC Interlocking Array Machined Sheet Boron Poly Beads Shield Detail